Pour lire la première partie: La qualité des moteurs, talon d’Achille de l’aviation française de 1940
Cherchez le coupable : enquête sur les causes de la faiblesse des moteurs français
Le défaut de fiabilité des moteurs français, aux conséquences pénalisantes pour les utilisateurs, tenait à des causes diverses, au premier rang desquels figuraient des problèmes de qualité des matériaux et de la fabrication mais aussi des erreurs de conception, résultant d’une orientation technologique sacrifiant la solidité à la recherche de la légèreté, à l’opposé des choix américains dictés par les impératifs de l’aviation commerciale.
C’est un thème récurrent dans la littérature que de constater que la qualité des moteurs français produits sous licence, notamment en Europe centrale, est supérieure à celle de la production nationale. Pour l’auteur, qui signe ***, d’un article de ‘La Revue de France’ publié en Aout 1938, « c’est ainsi que nos moteurs souffrent d’une infériorité, réelle celle-là, qui nuit, sinon aux performances, du moins à la longévité et à l’entretien : la médiocrité notoire des aciers français. A telle enseigne que des moteurs français fabriqués sous licence en Italie avec d’autres aciers, fournissent -c’est une exception- un meilleur service que le modèle »[60].
Deux facteurs principaux peuvent en effet être mis en cause: certes la qualité des métaux utilisés mais aussi la rigueur dans l’exécution des tâches. La première déficience est largement attestée. Ayant dû rebuter 5000 pistons et des séries entières de pièces forgées, Hispano demandait à n’être approvisionnée qu’en aciers fins d’importation: « l’examen de structure [des pièces rebutées] révèle, dans la plupart des cas l’inclusion de corps étrangers résultant d’un manque de soins ou d’incompétence du personnel chargé de l’élaboration du métal » [61].
«Quant à Weiller, si ses moteurs s’usent trop vite […], les fournisseurs nationaux d’aciers fins sont sans doute les principaux responsables », écrira après-guerre J.-L. Crémieux-Brilhac. Sur ce dernier point, en effet, « la production des aciers spéciaux nécessaires à la production des moteurs d’avions et des canons antichars ou anti-aériens plafonne et reste, pour une large part, sans qu’on ait beaucoup fait pour y remédier, de qualité défectueuse […] Les gros aciéristes ont toujours répugné à livrer des aciers fins qui exigeaient de lourds investissements pour un marché limité et un grand soin dans l’élaboration du métal » [62].
Devant la Sous-commission de contrôle des dépenses engagées du Sénat, le 9 Mars 1939, « le Ministre signale la défectuosité des matières premières et produits semi-ouvrés livrés à l’industrie aéronautique. L’aluminium et l’acier fourni par les usines françaises sont très irréguliers et les moteurs Hispano eux-mêmes présentent de grosses défaillance qui résultent tant de la matière première que des défectuosités de fabrication ». A titre d’exemples, les taux de rejets sur pièces estampées en alliage léger sont de 47% pour matières premières et de 12% pour défaut de fabrication, pour les pales d’hélices en dural respectivement de 32 et18%. En comparaison, note le ministre « J’ai commandé aussi 200 moteurs 12Y en Suède [sic-comprendre: en Suisse]. Ceux qui nous sont livrés sont excellents. Ceux qui ont été commandés en Tchécoslovaquie, [dont des 14 Mars] ne le sont pas moins. Or, ces modèles sont identiques à ceux fabriqués en France, mais ils sont nettement supérieurs au point de vue résistance et fabrication »[63].
En Juin, en réponse à une démarche sénatoriale, une note de la DTI relève alors la nécessité de soumettre les matériaux utilisés à un contrôle préalable en notant que « ce contrôle exige des opérations [telles que le recours aux rayons X] plus précises et plus délicates que celui permettant la mesure des qualités mécaniques des moteurs »[64] et une mission sur ce point est confiée à M. Guillet, membre de l’Institut. Le temps -ou la volonté- manqua cependant pour mettre en place les dispositions envisagées pour limiter cette source de faiblesse des moteurs français.
Un rapport de l’Inspection technique relevait en Mars 1940 : « la mauvaise tenue des segments, maladie chronique, parait actuellement en phase aigüe, non seulement sur 12Y mais sur tous les moteurs français. [Il en résulte une usure prématurée,] cause déterminante des défauts de compression et des pertes de régime»[65]. La fragilité des segments tenait sans doute au matériau utilisé, la régule, ce qui conduira à adopter des segments en bronze au plomb, qu’ Hispano va se procurer aux États-Unis, chez Allison.
Un autre facteur essentiel, en dehors de défauts de conception, tenait à une rigueur insuffisante dans l’exécution et le contrôle des tâches. Comme nous le verrons dans une étude à venir, le climat social avait indiscutablement affaibli l’autorité de la maîtrise, favorisant un certain laxisme conduisant à des malfaçons plus ou moins caractérisées. Le contrôle a posteriori s’exerçait certes, et une grande part des pièces défectueuses étaient rebutées, limitant la fréquence des défaillances sur les moteurs livrés, au prix d’un sérieux gaspillage de ressources, de main d’œuvre et de matières. La publicité de Gnome & Rhône communiquait d’ailleurs sur l’importance de ces rebuts comme une preuve du sérieux de qualité des produits de la maison.
Dautry, ministre de l’armement, traitant le 8 Février 1940 du problème des matières premières, dénonçait le gaspillage qui résultait de l’imprécision des fabrications, les rebuts et déchets dans la production de moteurs d’avion étant très supérieurs à leur niveau aux États-Unis[66]. Parmi les sources d’indisponibilité, figurait la mauvaise tenue des coussinets de tête de bielles en régule –alliage à base d’étain , qu’il faudra se résigner à remplacer : « l’utilisation de coussinets de bronze au plomb (qui sera entièrement fabriquée en France au cours de l’année 1940) a permis des augmentations de 10 à 25% de la puissance que l’emploi des coussinets de régule n’aurait pas autorisée »[67]. Dès Octobre 1938, un article signalait que les alliages type Allison, variété de bronze au plomb sans adjonction d’étain, « se sont répandus en Europe »[68].
Ce défaut de fiabilité et d’endurance était, comme nous le verrons, manifeste à l’égard de la plupart des moteurs anglo-saxons effectivement construits en série. Il ne semble pas l’avoir été globalement à l’égard des moteurs allemands. Le Daimler-Benz 601 du Messerschmitt 109, principal adversaire de l’Armée de l’Air, était limité à 100 heures d’utilisation entre révisions, durée encore réduite sur certaines versions plus poussées[69].
Certaines faiblesses des moteurs provenaient d’accessoires défaillants, comme l’illustre un exemple, choisi bien loin des avions d’armes habituellement considérés: le Salmson Cri-cri, un des principaux appareils équipant l’Aviation Populaire, connaissait un fort taux d’indisponibilité du fait de pannes affectant le réducteur de son moteur Salmson 9ADr de 60 cv, pour lequel les ingénieurs de l’entreprise avaient retenu un dispositif original, mais qui s’avéra déficient. Il ne s’agissait pourtant pas d’un moteur de pointe !
Une mutation inachevée
Particulièrement affectés, comme des pans entiers de l’industrie française par la crise de 1930, les motoristes n’ont eu ni les incitations à s’engager dans la mutation technologique touchant leur secteur, ni les moyens de la mettre en œuvre. De son côté, le ministère tardait à reconnaître les besoins d’accompagnement de l’industrie en termes de moyens d’étude et d’installations d’essais.
Au niveau de la conception et de la mise au point, les industriels comme les services officiels manquaient de moyens d’essais[70]. Ainsi, en Novembre 1938, le Comité du Matériel est informé que les essais du Pratt & Whitney n’ont pu commencer « du fait qu’un seul banc d’essai était disponible à la fois à Chalais Meudon et à Issy-les-Moulineaux»[71]. Certes, l’hebdomadaire « L’Usine » du 12 Mai 1938 annonçait l’ouverture prochaine d’un nouveau centre d’essai, à Orléans Bricy « disposant d’installations perfectionnées nécessaires aux essais complets de moteurs… en cours de réalisation et [qui] fonctionnera dès la fin de la présente année ». Les motoristes anglo-saxons recourraient largement à des dispositifs monocylindres permettant une analyse approfondie du cycle de fonctionnement du moteur et de ses accessoires, dispositif incontournable pour l’étude systématique des propriétés antidétonantes de différences essences. En visite aux États-Unis à l’automne 1937 l’ingénieur général Dumanois, ancien Directeur technique, en recommandait vivement l’adoption dans un rapport à Pierre Cot. Deux ans plus tard, des ingénieurs, retour de mission en Angleterre formulaient la même recommandation: « L’utilisation de monocylindres fonctionnant dans des conditions voisines de celles d’un moteur, permet seule de classer les carburants dans un ordre logique. Il importe donc d’en prévoir la construction immédiate en France pour l’étude du meilleur carburant nécessaire aux moteurs français»[72]. En deux ans, rien n’avait été fait !
On doit remarquer que, contrairement à la pratique en matière de cellules, l’Etat ne passe pas -ou plus- de commandes de prototypes de moteurs nouveaux. Il n’est dans ces conditions pas étonnant que les constructeurs privilégient une approche incrémentale, d’améliorations successives, même là où la formule de base apparait en voie d’être dépassée, comme pour les moteurs Hispano en ligne. Là où des modèles nouveaux sont développés, c’est avec des moyens insuffisants, d’où l’échec des Hispano 14 Aa et Ab, du Gnome-Rhône 18L, ou des projets Potez qui paraissaient à l’époque prometteurs.
On peut relever également des choix techniques discutables. Ainsi, parmi les facteurs de supériorité des moteurs américains en double étoile figurait leur vilebrequin à palier central, assurant un support intermédiaire réducteur d’effort et de vibrations. Loin d’avoir méconnu cette disposition, des motoristes français l’avaient testé et abandonnée. Quand le ministère de l’Air s’intéressera au Pratt &Whitney Twin Wasp, Barbarou fera valoir son antériorité, ayant ainsi équipé son 14 cylindres Antares de 1931[73]. Surtout, Clerget, qui avait doté son Diesel 14 E en 1934 d’un palier central sur rouleau, y renonce dans son modèle ultérieur 14 F, particulièrement réussi[74]. Cet épisode semble avoir pesé dans le désintérêt des motoristes français, comme des services techniques, pour ce dispositif qui devait être adopté tardivement sur les Gnome Rhône 14R et 14S à l’essai en 1940.
Quelques réalisations pourtant émergeaient dans ce contexte de mutation tardive: Nous avons déjà cité le cas des compresseurs Szyldowski qui, conservant la simplicité des compresseurs classiques, approchait les performances de compresseurs à deux vitesses et/ou à deux étages. On peut relever aussi le progrès constitué par la construction de la soufflerie Hipano-Suiza construite à Colombes en 1937 pour 7 millions. Elle permettait de tester des moteurs dans leur environnement aérodynamiques – fuselages de monomoteurs ou fuseau-moteurs pour les multimoteur- pour aider à résoudre les graves difficultés rencontrées en matière de refroidissement et à maitriser les phénomènes de compression dynamiques. On connait mal les résultats obtenus en 1938 et 1939, mais un témoignage de P. Satre atteste qu’au début de 1940, elle a permis de résoudre rapidement les problèmes de refroidissement rencontrés sur la Dewoitine 520[75]. Elle était aussi appropriée à l’étude du fonctionnement de moteurs en étoile, qu’Hispano développait également à cette époque[76]. Parmi les acteurs, le cas de Claude Bonnier est symbolique : ingénieur compétent en termes de recherche, homme courageux comme il le montrera dans la résistance, il était complétement à contremploi à la tête de la SNCM dont il maintenait la dispersion en matière de développement, sans maitriser les défaillances organisationnelles et industrielles.
A l’étranger, faisait-on mieux ?
Certains trouveront sévère le constat proposé des déficiences des moteurs d’aviation français en 1940. Une question mérite donc de retenir l’attention : faisait-on mieux ailleurs, chez notre principal adversaire et nos alliés anglo-saxons ?
L’industrie allemande devait s’avérer incapable de maintenir dans la durée, face aux alliés, la supériorité des moteurs de la Luftwaffe sur ceux de l’Armée de l’Air pendant la campagne de France. L’augmentation de puissance des Daimler-Benz allait s’accompagner d’une réduction de la fiabilité et d’une augmentation de la fréquence d’accidents. Cette industrie devait perdre la course à la puissance vis-à-vis de ses adversaires anglo-saxons. La tentative d’accoupler deux DB 601 en un DB 606 aboutit à un échec cuisant, répété sur près de mille exemplaires du bombardiers Heinkel 177 néanmoins produits. De son coté, BMW, qui produisait le BMW 801 du Focke-Wulf 190 , échoua complétement à réaliser un BMW 802 à 18 cylindres-formule du Gnome Rhône 18L ou du Pratt & Whitney R-2800, et surtout un 28 cylindres BMW 803, qui aurait été analogue au PW R-2360 Wasp Major.
La réussite anglaise elle-même, ne fut acquise qu’au prix d’une stricte concentration des efforts. En 1940, le Merlin était loin de tourner comme une horloge, suivant sa réputation d’après-guerre. Pour surmonter ses défis technologiques et industriels, Rolls-Royce concentra son effort sur ce modèle, en sacrifiant la mise au point de son ‘petit’ frère Peregrine, de son ambitieux Vulture à 24 cylindres et en retardant le développement de son successeur potentiel, le Griffon. De même, le succès du Hercules ne fut obtenu, après des retards entrainant la poursuite de la production du Mercury dépassé, que par l’abandon du développement de son ‘petit frère’ Taurus et d’un retard au développement et à la production de son ‘grand frère’ Centaurus. On peut par ailleurs douter de la pertinence du troisième programme de moteurs de la victoire, le Napier Sabre, qui payait son incontestable puissance d’une complication et d’une vulnérabilité pénalisante au regard des qualités d’un Centaurus ou d’un Pratt R-2800.
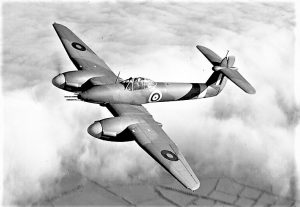
Le Westland Whirlwind, un beau chasseur victime de ses moteurs, source: wikipedia
Aux États-Unis même, les réussites incontestables, en termes de qualité comme de quantités produites, ont fait oublier une série d’échecs ou d’erreurs d’orientation aussi nets que celles rencontrées en Europe.
« L’armée comme la marine étaient convaincues en 1937 que les seuls moteurs de grande puissance de l’avenir seraient à refroidissement par liquide […] Arnold [chef d’état-major de l’Army Air Force] avait prévenu Pratt & Whitney que, si la société voulait des commandes de l’armée, elle devait développer un moteur refroidi par liquide », ce qui était l’avis de George Mead, vice-président de United Aircraft supervisant Pratt & Whitney[77]. Fait peu connu, Pratt devait poursuivre jusqu’en octobre 1940 le développement de moteurs X-1800/ XH/2600, à 24 cylindres en H, qui équipait divers prototypes comme le Curtiss XP-55 Ascender ou encore le Lockheed XP-58 Chain Lightning[78]. L’Army Air Force comptait aussi sur un continental XIV-1430 dont on espérait 1600 cv, prévu pour le Lockheed XP-49 et Wright faisait tourner un 42 cylindres à 7 rangs de 6. Devant délivrer 2300cv pour un diamètre de seulement 90 cm, ce moteur répondait au même projet que le Voisin 42M . Malgré sa puissance technologique, l’industrie américaine ne put mettre au point aucun de ces moteurs, les « moteurs de camions » en étoile développés pour les compagnies aériennes répondant largement aux besoins militaires. Seul moteur en ligne américain produit en grande série, l’Allison V-1710, après avoir été long à apparaitre en série, devait rester très moyen en termes de performances et de fiabilité. Certes, le turbocompresseur General Electric permettait au P38 de réaliser des performances compétitives mais, on le sait moins, cet équipement était à l’origine de nombreuses pannes, voire d’explosions de moteurs en vol. Le 27 novembre 1943 par exemple, 17 P38 durent abandonner leur mission d’escorte sur Berlin du fait de défaillances de leurs turbocompresseurs[79].
On le voit, ailleurs comme en France, le développement des moteurs d’avions ne suit pas un long fleuve tranquille…
Et si :
En matière de moteurs d’avions, rien ne se fait sans la durée. La marge de gain d’un scénario contrefactuel débutant en mars 1938, quand débute vraiment l’effort de réarmement aérien, est donc limitée.
Pour combler le handicap qu’allait constituer les moteurs pour l’aviation française de 1940, il faut revenir à l’origine des plans de réarmement aériens, en 1933-34. C’est en juin 1933 en effet, que le général Denain, voulant contrer une reconstitution menaçante de la Luftwaffe, lance le Plan I de rééquipement de l’Armée de l’Air prévoyant la mise en ligne de 1010 à un horizon de trois ans. On devait lui reprocher d’avoir mis la charrue avant les bœufs, comme le sénateur Amaury de la Grange, rapporteur du budget de l’Air le dira le 9 décembre 1937: « quand l’Allemagne a voulu passer de l’aviation de guerre camouflée à une véritable aviation militaire il y a trois ans […], nous avons tous passé par un moment d’affolement et le général [Denain] a passé en 1934 une commande formidable espérant résoudre le problème à coup de crédits et nous avons commis l’erreur de l’y pousser. Nous aurions dû à ce moment-là constituer, comme on l’a fait en Allemagne, la base de nos industries aéronautiques, c’est-à-dire faire des surfaces couvertes, acheter l’outillage, organiser nos usines, nous ne l’avons pas fait »[80].
Nous aurions aussi dû adopter un programme ‘moteurs’, actualisé au rythme des plans qui vont se succéder jusqu’en 1939. Les principales modalités de ce plan ressortent des constats et analyses qui précédent :
– développer les moyens d’études et d’essais, par l’accroissement et le rééquipement des centres de Meudon et d’Issy, ou par la création d’un centre nouveau comme celui qui allait voir le jour à Bricy, en étant attentifs à ce qui se réalisait outre-Atlantique ;
-appliquer des épreuves de qualification plus strictes, mettant en œuvre des essais au banc comme en vol, dont l’utilisation de moyens renforcés éviteraient qu’ils ne prennent trop de temps ;
-établir des programmes de moteurs puissants, avec un dispositif de financement graduel : une première tranche, modeste, sur dossier, une seconde, pour la commande de prototypes, une troisième, plus incitative, conditionnée aux résultats de l’homologation.
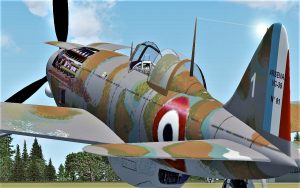
Chasseur brillant, l’Arsenal VG 39 laisse apercevoir son moteur HS 12Z, source: flightsimulator
Ce dispositif aurait dû être complété de mesures relatives à la modernisation des moyens de production, qui ne relèvent pas de l’objet de la présente étude.
Il n’est pas besoin de rêver pour estimer qu’un tel dispositif aurait changé la donne pour la motorisation des avions français de 1940 : chez Gnome et Rhône, des 14N fiabilisés seraient sortis en série dès 1939, leur relève par des 14P, intervenant au printemps 1940 et par des 14R au point à la fin de la même année. Les dernières séries de Morane et les Dewoitine 520 auraient disposé de HS 12Y 51 ou équivalent de plus de 1000 cv, et l’Hispano ‘4 soupapes’ 12 Z aurait alors atteint un stade avancé de mise au point. Les ‘18 cylindres’ auraient commencé leurs essais en vol, mais l’Hispano 14AA, correctement développé et mis en production, délivrant les 1300 cv correspondant au potentiel minimal de sa cylindrée, aurait pu sortir en série.
Les protocoles d’essais plus approfondis des moteurs auraient aussi conduit à l’adoption plus rapide de radiateurs performants, d’échappement à effet propulsifs et, sans doute, du compresseur Szydlowski.
Dans un tel scénario contrefactuel, le recours à l’étranger aurait pu être limité, à des équipements d’essais et à des licences spécifiques de dispositifs ou composantes, ainsi bien sûr qu’à des machines-outils dont certaines n’étaient pas disponibles chez les producteurs nationaux.
Notes et références.
[60] La France refera t’elle son aviation ?, La Revue de France, 15-08-38, p. 142.
[61] Cf. J. L. Crémieux-Brilhac, Les Français de l’An 40, p. 92, aussi pour citations suivantes.
[62] Le fournisseur de Salmson en ébauches n’utilise que des aciers suédois !.
[63] Cf. Note « Mauvaise qualité des matières premières », in Fonds Guy la Chambre, 11Z12932.
[64] « Contrôle des matières premières chez les fabricants de moteurs », note non datée, SHD 11Z12939.
[65] Rapport du 26-03-40, in SHD 1D51.
[66] Rapporté in SHD 11Z12943.
[67] Document DGT du 8-12-39, in SHD 11Z 12932.
[68] La Technique Moderne, 1938, n°21, p.723.
[69] Cf. Isby, The Decisive Duel, p. 192.
[70] La soufflerie Hispano Suiza constituait une exception. Elle devait permettre, tardivement, de régler sur le VG33 les problèmes de refroidissement rencontrés sur le MS 406 et, pendant près d’un an, sur le D520.
[71] PV du CoMat 26-11-38
[72] Cf. Rapport de mission des représentants du Comité des carburants, 26 novembre-3 décembre 1939. SHD 2B161.
[73] Son argument, relayé par Laurent Eynac, est l’occasion pour les services du ministère de contester que le Pratt & Whitney surclasse les moteurs Gnome récemment mis en service, ainsi que la supériorité de principe du vilebrequin palier central, Juin 1939, SHD 11Z12939.
[74] Cf. G. Hartman, Mazout d’enfer, document en ligne, pp. 4 et 5.
[75] Déposition à l’instruction du procès de Riom.
[76] J. Valensi, Les laboratoires d’aérodynamique Hispano-Suiza, in Revue Technique Hispano-Suiza, Janvier 1939, p. 34.
[77] Mc.Cutchen, No Short Days, p.I-4.
[78]W. Green, War Planes of the Second World War, Fighters, vol Four, pp. 62 et 124.
[79] Paul Ludwig, Development of the P51 Long-Range Escort Fighter,pp. 181, 183.
[80]Cité par T. Vivier, La politique aéronautique militaire de la France, janvier 1933-septembre 1939, p.189.